How to Select the Storage Tank for your Edible Oil processing Plants
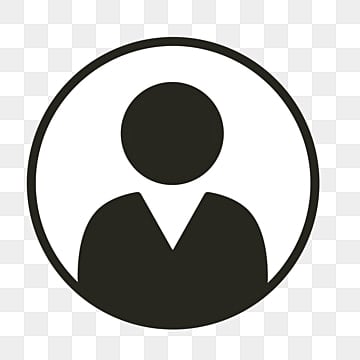
Riyaz Tunvar
Riyaz is the Sales and Marketing Director at N&T Engitech Pvt. Ltd., a leading manufacturer and supplier of complete edible oil plants and machinery. With extensive expertise in the oil and fats industry, Riyaz and his team provide high-quality solutions for processing various types of oil seeds, tailored to meet the unique needs of clients worldwide.
Build Something People Want
Let's talk about your engineering needs to find the best solutions.
Submit Your Business Inquiry
Are you interested in learning more about our technologies? Feel free to contact us right away to discuss your project.