Types of Warehouses: Which Is Best For Your Industrial Usage
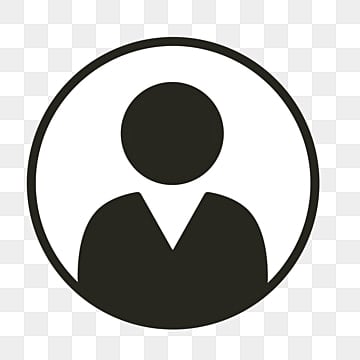
Ahmad Tunvar
Ahmad Tunvar is the EPC Head at N&T Engitech, where his dynamic leadership and extensive experience drive the company’s success in engineering, procurement, and construction projects. Ahmad plays a vital role in the growth of N&T Engitech’s EPC initiatives, setting new industry benchmarks with his strategic vision and hands-on approach.
Build Something People Want
Let's talk about your engineering needs to find the best solutions.
Submit Your Business Inquiry
Are you interested in learning more about our technologies? Feel free to contact us right away to discuss your project.